In this article
Every year, workplace accidents involving lifting equipment lead to serious injuries and even fatalities that could have been prevented. A safe workplace benefits everyone, employees stay healthy, employers avoid costly incidents, and businesses can build and maintain a strong reputation. Whether you’re a site manager, safety officer, or equipment operator, understanding LOLER is vital as it isn’t just about compliance, it’s about saving lives.
Before LOLER 1998, lifting equipment safety was governed by a mix of older laws, with the Factories Act 1961 being the most significant. LOLER modernised and consolidated these rules in order to improve safety standards for lifting equipment and operations in the workplace. It was implemented in response to accidents and fatalities that were caused by poor maintenance, inadequate inspection, and unsafe use of lifting equipment.
Before LOLER regulations, there were frequent accidents involving lifting equipment due to poor maintenance and lack of procedures. Existing laws, such as the Health and Safety at Work Act 1974 covered general workplace safety but lacked specific rules on lifting operations. LOLER ensured all lifting operations were properly planned, supervised, and carried out safely. It also aligned with European health and safety laws, particularly the EU Work Equipment Directive.
LOLER was part of a wider effort to reduce injuries and fatalities related to lifting operations, ensuring equipment was fit for purpose and used correctly. It remains a key regulation in industries such as construction, manufacturing, and warehousing.
What is LOLER?
The Lifting Operations and Lifting Equipment Regulations (LOLER) regulations 1998 is a critical piece of legislation designed to ensure the safe use of lifting equipment in the workplace. The LOLER regulations 1998 are enforced under the Health and Safety at Work Act 1974. LOLER places responsibilities on employers, people who are self-employed, and those in control of lifting equipment to ensure that operations are planned, supervised, and carried out safely.
The key elements of LOLER include:
- Ensuring equipment suitability – lifting equipment must be appropriate for the task and safe for use.
- Competent personnel – operations involving lifting must be conducted by trained and competent individuals.
- Regular inspections – equipment must be examined by a qualified person at specified intervals. Regular inspections help to identify hazards before they cause harm, reducing workplace injuries and fatalities.
- Clear markings – lifting equipment must display safe working loads and any other necessary information.
- Minimising risk – lifting activities must be planned to prevent accidents, including load falling or equipment failure.
LOLER regulations are designed to reduce the risks associated with lifting operations and ensure that equipment is used correctly, safely, and maintained properly. LOLER aims to prevent workplace accidents and injuries related to lifting operations. Lifting equipment, such as cranes, hoists, lifts, forklifts, and even slings and chains, poses significant risks if they are not used correctly. LOLER ensures that:
- Equipment is strong and stable enough for the intended use.
- Lifting operations are properly planned and supervised.
- Loads are safely secured in order to prevent falls or swinging.
LOLER places legal obligations on employers, self-employed people, and those in control of lifting equipment. Compliance with these regulations is mandatory under UK law, and failure to adhere can lead to:
- Legal action and fines from the Health and Safety Executive (HSE).
- Increased liability in the event of an accident.
- Criminal prosecution if negligence leads to injury or death.
Employers have a duty of care to protect their workers, and LOLER provides clear guidelines to ensure safety is a priority. LOLER not only safeguards employees who operate or work around lifting equipment but also protects the public and anyone who may be nearby. Poorly managed lifting operations can result in dropped loads, collapsing cranes, or runaway forklifts, endangering bystanders. By enforcing strict regulations, LOLER minimises these risks. When employees feel safe, they are more likely to follow protocols, use equipment correctly, and stay alert to hazards. Fear or stress can lead to distraction, rushing, and mistakes which are major causes of workplace accidents.
Non-compliance with LOLER can lead to severe financial and reputational consequences for businesses, including:
- Compensation claims from injured workers.
- Increased insurance premiums.
- Loss of business reputation due to unsafe practices.
LOLER works in conjunction with other health and safety regulations, such as:
- The Health and Safety at Work etc. Act 1974 – this is the primary legislation governing workplace health and safety in the UK. It places a duty on employers to ensure, as far as is reasonably practicable, the health, safety, and welfare of their employees and others affected by their work activities. The key provisions include, providing a safe working environment, adequate training, risk assessments, and appropriate safety measures, places a duty on employee’s to take reasonable care of their own and others’ safety and comply with workplace safety policies. Employers must identify and mitigate workplace hazards and ensure access to facilities such as toilets, drinking water, and first aid. The Health and Safety Executive enforces the Act through inspections, investigations, and prosecutions. The Act applies to all workplaces, including offices, factories, construction sites, and public spaces. Non-compliance can lead to legal action, fines, or imprisonment.
- PUWER – this is a UK regulation designed to ensure that work equipment is safe to use and properly maintained. It applies to employers, the self-employed, and those responsible for work equipment. The key Requirements of PUWER 1998 include ensuring that equipment must be appropriate for the task and used in suitable conditions, regular inspections and servicing to keep equipment safe, ensures that workers must be adequately trained to use equipment safely, safety measures for equipment including having clear safety signs and warnings and sets out that equipment should be used in a safe environment to minimise risks. PUWER applies to all workplaces where equipment is used, including factories, construction sites, offices, and farms. It complements other health and safety laws, such as the Health and Safety at Work Act 1974, ensuring that work equipment does not pose risks to users or others. The legislation covers all work equipment, including lifting devices.
- The Management of Health and Safety at Work Regulations 1999 – is a key piece of UK legislation that builds on the Health and Safety at Work etc. Act 1974, requiring employers to proactively manage health and safety risks in the workplace. The key requirements are that employers must assess workplace risks to employees and others who may be affected, employers must implement measures to eliminate or reduce risks, suitable management systems must be in place, employers must appoint competent individuals to assist in health and safety management, employees must receive adequate health and safety training, employers and self-employed individuals must work together where necessary, there should be additional protections for young workers, new or expectant mothers, and temporary workers. The regulations are designed to create a structured approach to workplace health and safety, ensuring hazards are managed effectively.
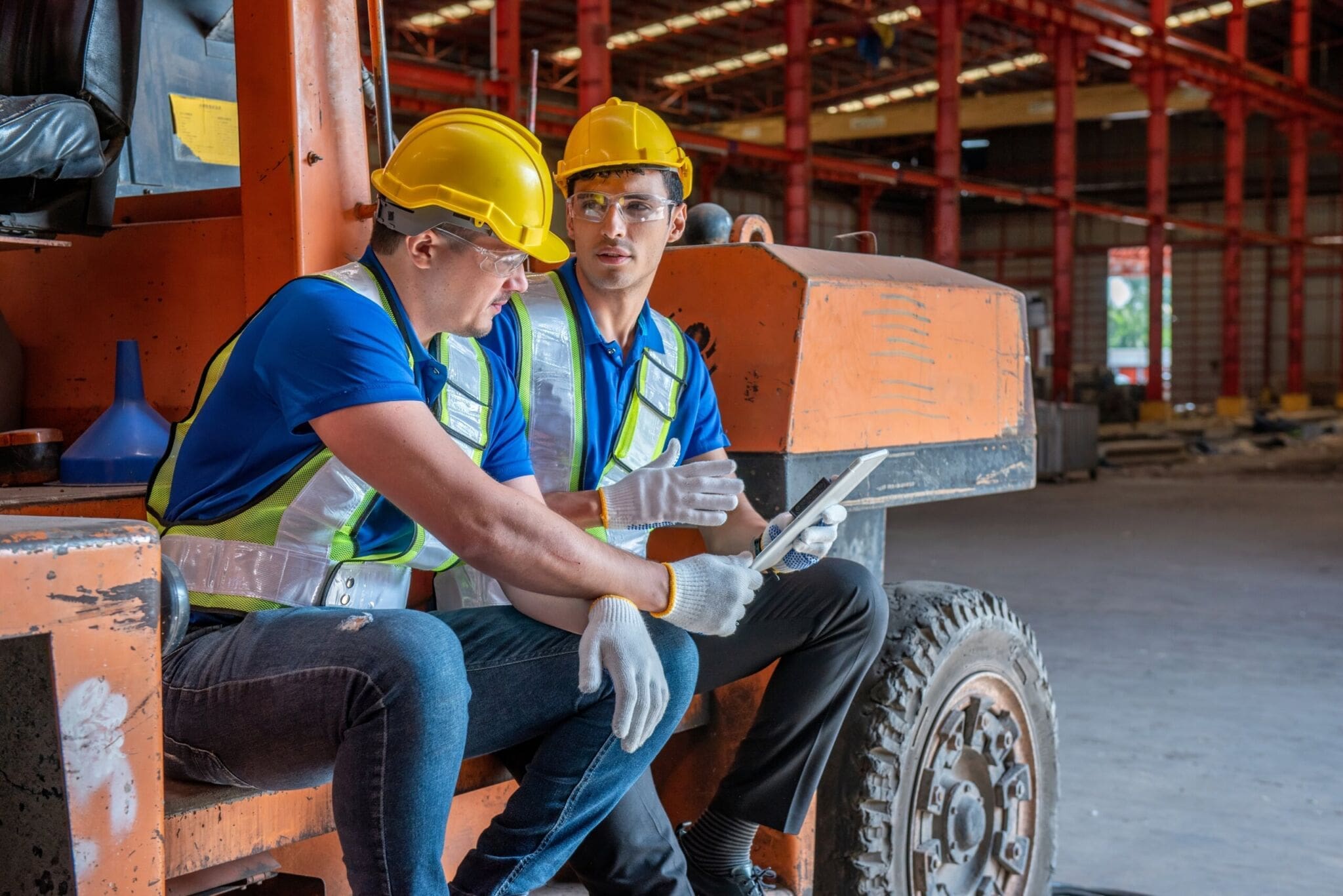
What Are the 3 Principle Aims of LOLER?
The three principle aims of LOLER are:
- To ensure that lifting equipment is suitably strong and stable – equipment must be designed, constructed, and capable of safely handling the intended loads. It must be marked with its Safe Working Load and properly maintained in order to prevent failure.
- To ensure that lifting equipment is safely positioned and installed – equipment must be set up correctly, for example cranes on stable ground and hoists securely fixed. The environment must be hazard-free, including avoiding overhead power lines or unstable surfaces.
- To ensure that lifting operations are properly planned, supervised, and carried out safely – every lift must be risk-assessed and planned by a competent person. Operations must be supervised to prevent unsafe practices for example overloading or improper slinging. A risk assessment is a process designed to identify hazards, evaluate risks, and implement control measures in order to prevent harm. The key purposes of a risk assessment is to identify hazards, recognise potential dangers for example unstable loads, faulty equipment or unsafe environments, evaluate risks to determine the likelihood and severity of harm and implement control measures. Risks can then be reduced to an acceptable level to prevent accidents and injuries.
What happens during a LOLER Inspection?
Regular inspections, referred to as thorough examinations under LOLER, are a legal requirement to verify the safety and functionality of lifting equipment. These examinations should be carried out:
- Before the first use – for new equipment or after installation.
- At regular intervals – typically every 6 months for equipment lifting people and every 12 months for other equipment. These intervals may vary based on risk assessments or manufacturer recommendations.
- Following exceptional circumstances – if an incident, damage, or environmental condition has or may have impacted the equipment’s integrity.
Inspections must be conducted by a competent person, which is often an independent examiner. This is to ensure an unbiased and thorough review. Records of these inspections must be maintained for future reference and compliance checks.
The competent person, a qualified inspector should carry out pre inspection checks and also review:
- Equipment records, including past inspections and maintenance logs.
- Manufacturer’s instructions and specifications.
- Any reported defects or incidents.
The visual & functional examination should include:
- Structural integrity, checking that there are no cracks, corrosion, or deformities.
- Mechanical components including wire ropes, chains, hooks, and brakes for wear/damage.
- Safety devices including limit switches, overload alarms, emergency stops.
- Load markings checking that the safe working load is clearly displayed.
- Installation and stability, checking that there is proper anchoring for fixed equipment or outrigger deployment for cranes.
Operational testing should be completed if required. The equipment may be tested under load, where safe in order to verify functionality. Movement, lifting, and lowering mechanisms should be checked for smooth operation.
The inspector provides a written report, this is required by law and should detail:
- Any defects or safety concerns.
- Necessary repairs or actions.
- The next inspection date.
If the equipment is unsafe, it must be taken out of service immediately.
A LOLER certificate is a document provided following a thorough examination of lifting equipment. It indicates that the equipment complies with LOLER standards and is safe for use. While not explicitly named in the legislation, certificates are commonly issued by inspection bodies or competent persons as proof of compliance.
Key details on a LOLER certificate include:
- Description of the equipment.
- Date of the examination.
- Results of the inspection.
- Recommended date for the next examination.
- Name and qualifications of the examiner.
Employers must retain these certificates and make them available for inspections or audits. Workplaces are not explicitly required to appoint a designated LOLER person. However, having a designated competent person responsible for LOLER compliance is considered best practice and will make things easier if problems arise.
Why was LOLER brought into action?
LOLER was introduced to save lives by ensuring lifting equipment is safe, well-maintained, and properly used. Before LOLER, lifting-related accidents were common due to poorly maintained equipment, overloading and lack of proper inspections. LOLER enforced strict safety checks in order to prevent equipment failure and injuries. Its purpose was to:
- Modernise outdated laws – previous regulations like the Factories Act 1961 were too vague and didn’t cover modern lifting equipment. LOLER provided clear, specific rules for all lifting operations, including cranes, forklifts, hoists, scaffolding hoists, vehicle tail lifts. The UK was required to implement the EU Machinery Directive and Use of Work Equipment Directive (AUWED) and LOLER incorporated these into UK law, ensuring that there were consistent safety standards across Europe.
Many accidents occurred due to poorly planned lifts or untrained workers, and before LOLER, some companies’ neglected maintenance in order to cut costs.
Since its introduction, LOLER has:
- Reduced lifting-related accidents in construction, manufacturing, and logistics.
- Standardised safety practices across industries.
- Improved equipment lifespan by enforcing maintenance.
- Prevented legal loopholes that allowed for unsafe practices.
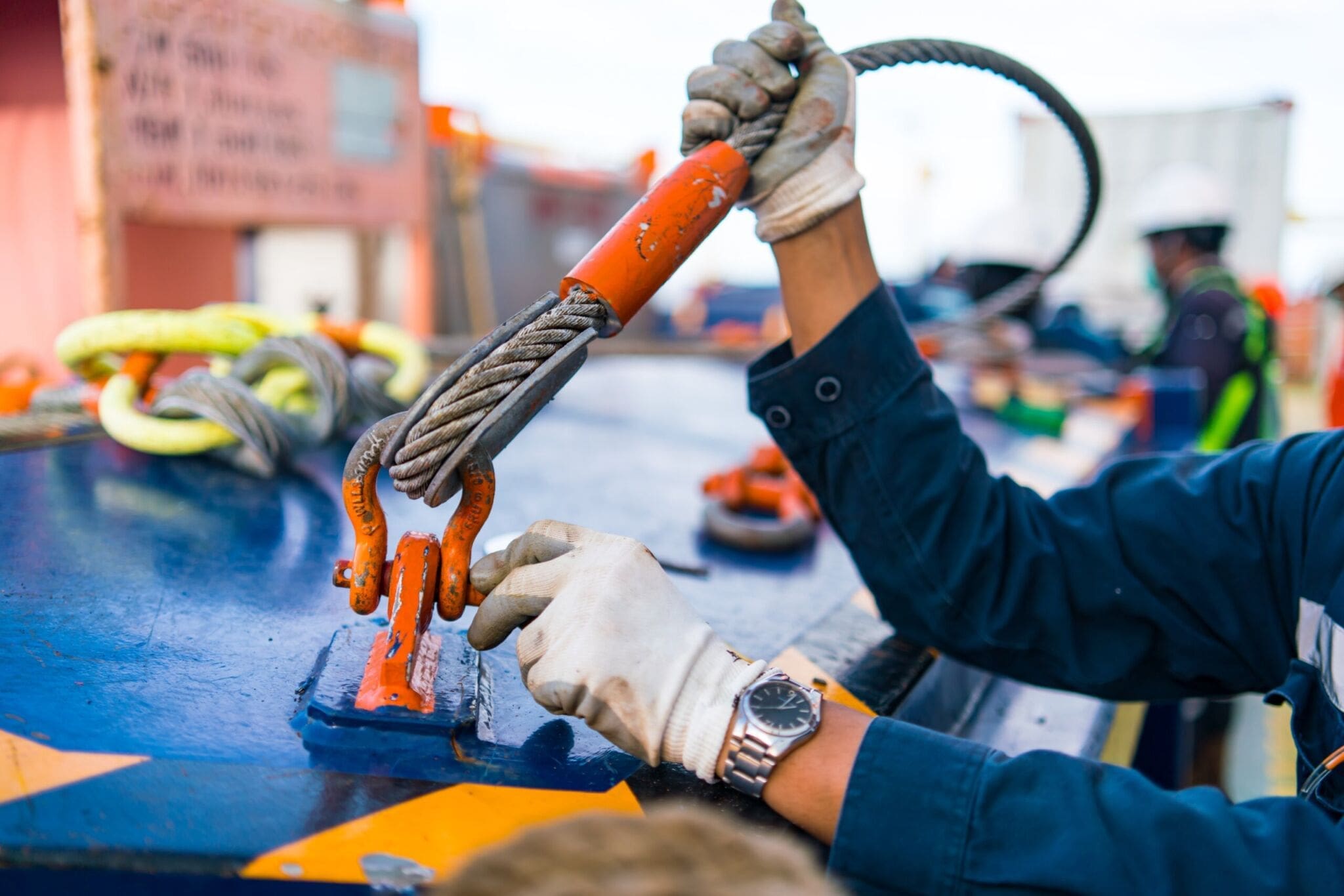
Obligations under the LOLER Regulations
The LOLER Regulations 1998 place specific legal duties on employers, equipment owners, and those controlling lifting operations. These obligations ensure that lifting activities are conducted safely in order to prevent accidents and injuries.
The key responsibilities include:
- A duty to ensure that equipment is safe and suitable – all lifting equipment must be strong and stable enough for its intended use, marked with its safe working load (SWL) and regularly inspected and maintained in order to prevent failure.
- Thorough examinations by a competent person – mandatory inspections are to be completed every 6 months for lifting equipment or 12 months for accessories like chains and slings. Examinations must be recorded, with defects reported immediately.
- Proper installation and positioning – equipment must be installed or positioned to minimise risks, for example cranes on stable ground and hoists securely fixed. Environmental hazards like overhead power lines must be avoided.
- Training and competency – only trained and competent personnel should operate or supervise lifting equipment. Workers must understand load capacities, safety checks, and emergency procedures. Workplaces should have clear emergency procedures in case of equipment failure and ensure workers know how to respond to load drops, equipment malfunctions, or injuries.
- Record-keeping and documentation – employers must maintain inspection reports from thorough examinations, maintenance logs of repairs or modifications, training records and proof of competency.
Failure to comply with these can lead to enforcement action, fines, or prosecution under the Health and Safety at Work Act 1974. Both the employer and individual workers can face prosecution if they fail to comply with safety duties, but the primary legal responsibility falls on the employer.
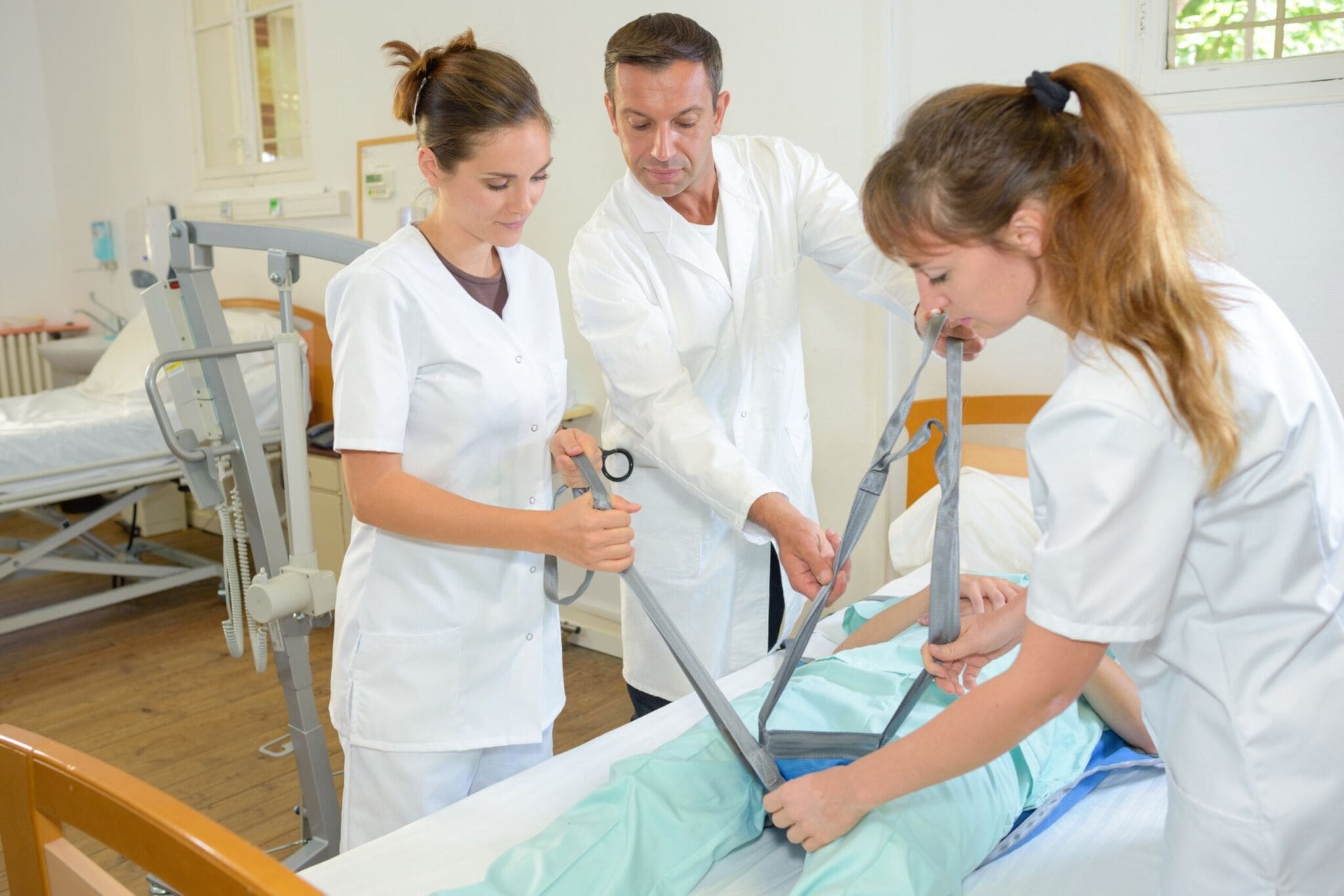
Planning, organising and carrying out lifting operations
LOLER requires that every lifting operation is properly planned, supervised, and executed safely in order to prevent accidents.
Key steps in safe lifting operations includes:
- Risk assessment and planning – a competent person must assess the weight and nature of the load, which lifting equipment is needed, environmental factors such as weather, ground stability, or obstructions. A written lifting plan may be required for complex lifts. A LOLER-compliant lifting plan is a structured document that ensures safe execution of lifting operations. It is legally required for complex lifts and strongly recommended for all high-risk activities.
- Selection of appropriate equipment – this means that equipment must be rated for the load and never exceed the SWL, be inspected before use and have no defects. It should also have suitable attachments including the correct hooks, slings or spreader bars.
- Supervision and communication – a designated person must supervise lifts, especially if the lift is high-risk, for example heavy loads or confined spaces or multiple workers are involved. Clear hand signals or radio communication must be used.
- Safe execution of the lift – the lift should be tested with a small elevation to check balance. There should be smooth, controlled movements with no sudden jerks or swings. There should be exclusion zones to keep unauthorised personnel away from the area.
- Post-lift checks – equipment should be inspected for damage after use. Any issues must be reported and repaired before reuse.
By enforcing strict standards for equipment safety, thorough inspections, and properly planned lifts, LOLER reduces the risks of serious accidents and fatalities in workplaces across the UK.
For employers, compliance isn’t just about avoiding fines, it’s about protecting your employees. For workers, it ensures they return home safely every day. Whether you operate cranes, hoists, or forklifts, understanding LOLER helps create a culture where safety is prioritised.